Cristina Leon Vera | 08/05/2025
When a company begins operating, it must comply with certain security levels established by the relevant public administration by obtaining a license to operate. This license is justified by a project that defines minimum security levels in accordance with current regulations.
These safety levels essentially depend on the following aspects:
- The activity in question
- Characteristics of the establishment and its environment
- The inherent risks of the activity, assessing the danger and combustibility of the materials used
- The facilities where the activity is carried out
Regulations and norms evolve over time as a result of lessons learned from past incidents and the development of more advanced systems, which contribute to improving established safety guidelines. As such, different levels of security may be required today compared to the licenses granted for the same activity in previous years. These levels may also vary depending on the geographic location of the company in question, due to the application of local or national regulations.
When clients receive a report listing improvement measures to be taken following an inspection by the insurer, confusion may arise as a result of not fully understanding why the insurer is issuing a report with recommendations when the client is already in compliance with all the relevant regulations pertaining to their activity. This article seeks to clear up that confusion.
As part of our work on each inspection visit, insurers focus on advising clients on following the best safety guidelines recognized in their particular sector, based on international standards and best practices adopted across the industry. We make use of all available knowledge, so the recommendations are not necessarily linked to national regulations, nor are they limited by geographic location. These set of recommendations is presented to the client in the form of an improvement plan, the objective of which is to promote excellence in risk management in their industry, beyond merely meeting the requirements related to their activity.
Construction/passive protection
The type of construction used by a company at its facilities is crucial in assessing its fire risk, and there are three important aspects to consider: the stability of structural elements against fire, the fire resistance levels of the products used and how the structure is subdivided.
When starting, every company must guarantee a minimum degree of stability in its load-bearing structure against fire. This can be done by applying a steel coating on reinforced concrete structures or by encapsulating metal structures. Even if this aspect is completely guaranteed when the company starts operating, it doesn’t mean that this will always be the case – a company’s facilities are in constant use and are exposed to unforeseeable blows and damage from vehicles and machinery, as well as modifications that are not done properly.
As a result of the foregoing, it’s vitally important to know the risks associated with the construction materials to be used. As is well known, wooden linings and sidings are highly combustible. It’s not so well known however that expanded polystyrene core (EPS) sandwich panels are also combustible and can be even more dangerous. EPS has a lower combustion point (100-120°C) compared to wood (270-280°C), which means that EPS generates combustible vapors (burning) at a lower temperature than wood. In addition, it’s important to know the classification of reaction to fire of the products that are installed or applied, since a poor classification of smoke opacity or falling droplets means that some materials generate more opaque smoke and flammable particles in the event of a fire, which spreads in the event of a fire.
Furthermore, in order to delay or extinguish a fire, establishments are divided into fire sectors. These sectors are created based on the fire load of the activity, i.e., based on the fire resistance levels of the materials enclosing the spaces and the maximum surface area required to create obstacles that slow the spread of the fire. However, it’s common to find that these areas do not guarantee the fire resistance they were designed for, due to unsealed gaps and/or steps, or firewalls that don’t close properly. It’s essential to know the distribution of these sectors in each company and take the necessary precautions when making modifications to ensure that essential levels of protection are maintained.
Fire protection
Fire protection installations are defined for each activity according to the type of establishment, fire resistance and surface area and type, and are detailed in the activity license for the project that establishes initial protective measures.
Companies generally evolve, change and adapt constantly to remain competitive. As such, it’s not unusual for them to make modifications to adapt to their new needs, and unfortunately on many occasions, adapting fire protection installations are left to one side.
Much of the time spent on our inspections is to assess whether the fire protection measures in place are appropriate for the risk being protected. One common case we come across is storage in areas originally considered for other purposes. At some point, production areas were converted into storage areas without considering how that space functions in terms of resisting fire.
This is an extremely important point. For example, in a lumber factory, a process area with sprinkler coverage can be perfectly protected with a water density of 5 l/min. However, if part of this same area is used to store raw materials or finished wooden products, it could require a density of up to 12.5 l/min (considering solid shelves for storage up to 5 m high), which is more than twice the level initially planned for. Storage height also affects protection levels: in this same company, with sprinkler protection for a warehouse designed for a maximum height of 3.4m (water density of 7.5 l/min), about 2-3 racks of pallets, increasing the number of racks to four would raise the required water density to 12.5 l/min, an increase of 66%.
As such, it’s important to emphasize that installing a sprinkler system doesn’t mean that a company is fully protected against any hazardous scenario. As in the two examples above, the company’s new storage needs were not properly evaluated, and its water-based sprinkler requirements are much higher than what was initially provided for. However, the automatic extinguishing system using water sprinklers can usually be adapted to a company’s new needs.
Prevention
In the beginning, regulatory requirements stipulate that clear, detailed and well-executed risk prevention procedures be in place to guarantee safety. These procedures are based on local regulations and tend to focus mainly on occupational risk prevention, offering less detail on other important aspects with respect to international standards.
This is especially evident in the field of fire protection, where inspections, tests and maintenance demand broader routines and scopes to ensure optimal system operation and prevent critical failures. A clear example of this situation is the fire protection group’s pressure/flow curve test. This is a periodic test that evaluates that the performance is adequate according to the nominal characteristics. This is a basic practice, established in regulations in many countries and international regulations, but it is not mandatory in several Latin American countries. The reason we insist on this recommendation is that these tests allow for the performance of equipment to be evaluated at key points, to detect deviations and determine the necessary adjustments or maintenance to guarantee reliability.
In the same vein, another common scenario concerns the failure to implement an out-of-service management procedure for fire protection systems, given that it’s vital to supervise the safe disconnection of protection systems and implementation of alternative safety measures to control or mitigate a potential fire where fire protection systems don’t function correctly.
Both cases presented clearly illustrate the diversity of regulatory requirements for industries, which don’t always establish practices considered to be basic prevention. These measures, although recommended in numerous recognized standards, are not mandatory in certain countries.
In the insurance arena, we use these standards as a basis for our recommendations, in order to inform clients about prevention practices that improve safety levels in their industries.
Emergencies
A company’s emergency management system is described in its self-protection plan. This plan includes the analysis and evaluation of the risks in question, as well as the scenarios that could be affected by an emergency. It also defines the available resources, and detailed prevention, alarm, evacuation and relief action items. It also specifies how to maintain the effectiveness of the plan, its implementation, drills and updating.
During risk inspections, we often find that the self-protection plan is not fully updated or correctly implemented. After reviewing the plan with the client, we observe that the teams have changed or that new facilities and renovations have not been included in the plan. However, regular evacuation drills are usually carried out, managed by the emergency team and executed by the evacuation team.
Despite this, we notice that no theoretical or practical training is carried out on the handling of fire protection equipment. This training is essential for staff so that they are prepared to use firefighting equipment effectively in case of emergency. The key to successfully tackling a fire is acting during its early stage, before it starts to spread, which can take just a few minutes. An appropriately trained intervention team significantly increases the chances of success.
As such, as part of our inspection, we evaluate the training content, which generally doesn’t include simulations on how to use firefighting equipment. These practices are essential for intervention personnel to successfully combat a fire in its early stage, before the situation becomes uncontrollable and too dangerous to fight with the existing resources available in the company. It’s also advisable to contact nearby emergency teams, such as firefighters, and invite them to attend the practice drills so they get to know the company’s facilities.
In conclusion, we believe it’s essential to explain that various aspects of the mandatory conditions established in a company’s activity license are either outdated or insufficient, or need to be expanded on the basis of numerous other reasons. Our objective is to always advise our clients holistically and comprehensively so they can understand, identify, mitigate and protect their companies more effectively, always on the premise that these recommendations are not mandatory, but are oriented toward adopting industry-wide best practices.
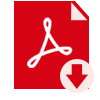