Gonzalo Sanz Segovia | 09/07/2025
Could greater automation and robotization result in a lower loss ratio in manufacturing industries?
Digital transformation and process automation have been key elements in the modernization of manufacturing. However, their impact on claims experience – understood as property damage, machinery breakdown and business loss – is a topic that has received less attention than how these elements have impacted human occupational safety. This article analyzes the relationship between automation and technical claims, based on specialist literature, case studies and guidelines from industrial insurers. It is proposed that, while robotization reduces certain types of claims, it also introduces new risks that must be managed using complementary technologies and new maintenance strategies.
Since the mid-2000s, industrial automation has experienced significant growth, driven by advances in digital technologies, robotics, artificial intelligence and connectivity.
In the context of the so-called Industry 4.0, automation, robotization and digitalization have become fundamental pillars of industrial competitiveness. Modern plants integrate SCADA (Supervisory Control and Data Acquisition) systems, collaborative robots, smart sensors and predictive maintenance to boost production efficiency. Although operational benefits are evident, the implications of these elements on technical claims levels have not received sufficient attention in the literature or risk management practices.
This article seeks to understand the relationship between the degree of automation in the manufacturing industry and the frequency, severity and type of technical claims observed.
Automation involves replacing repetitive, dangerous or highly demanding human tasks with programable mechanic systems. Automation can be classified by increasing levels of sophistication, from the use of basic sensors to cyber-physical systems interconnected with artificial intelligence.
Typical components include:
• Industrial and collaborative robots
• Programmable logic controllers
• Digital supervision and control systems
• Software for executing company manufacturing
• IT communication networks
• Connected sensors and actuators
These elements generate new technological dependencies that can affect the resilience of production systems. For the purposes of this study, technical claims are understood as the occurrence of events that cause:
1. Property damage to infrastructure and facilities
2. Breakdown of critical machinery or equipment
3. Business interruption with an economic impact
Several studies of industrial insurance companies (such as FM Global, Allianz and Zurich) show that automation can have positive effects on the reduction of claims in the following aspects:
• Accuracy and repeatability: errors causing collisions or breakages due to incorrect handling are reduced.
• Less human intervention: reduces the risk of bodily injury arising from misuse of machinery or manual disconnections.
• Predictive monitoring: sensors can detect overheating, vibrations or leaks before they result in serious breakdowns.
• Redundancy and remote control: improves the ability to respond to incidents and makes it possible to isolate faults before they escalate.
Companies like Bosch, Siemens and Nissan reported improvements in operational continuity and a reduction in the number of breakdowns after implementing IoT-based predictive maintenance solutions.
However, the same technology introduces new risks, including:
• Software faults: a programming error or improperly implemented update can cause a production line to stop completely.
• Communications dependency: an industrial network failure may render a whole system inoperative.
• Cyber attacks: connected plants are vulnerable to ransomware or sabotage that could affect production.
• Incorrect diagnosis: defective sensors may cause unnecessary stoppages or overlook dangerous conditions.
• Specialized maintenance overload: requires highly qualified personnel to fix, the absence of whom could delay recovery after a serious incident.
The foregoing factors require a risk management strategy adapted to the new technical reality.
Various risk reports show that manufacturing plants with a high degree of automation tend to have a lower claims frequency, but that when they do occur, they have a higher financial impact.
A study by Swiss Re (2022) indicates that failures in automated systems represent 28% of the value of industrial claims, compared to only 15% in non-automated plants. The explanation is that failures affect more integrated systems that are more expensive to repair in the event of an accident or failure.
In a case analyzed by FM Global, a fully robotic packaging line in a food plant suffered a complete stoppage due to a firmware failure. The time taken to restart the line was nine days, generating business interruption losses in excess of 2 million euros, even though there was no significant material damage to the line itself.
The key to reaping the benefits of automation without aggravating or provoking technical claims lies in proactive risk management. Some recommendations include:
• Redundant design of critical systems
• Specific electrical and fire prevention protection features for electronic equipment
• Segmentation of industrial networks to prevent the spread of faults
• Industrial cybersecurity audits
• Continuous training in predictive maintenance and asset management
• Integration of digital supervision systems and risk analysis software
The implementation of automated systems has contributed to reducing operational errors and has improved process accuracy, which can reduce certain types of failures and breakdowns.
Automation in itself is not intrinsically risky, but it does change the nature of industrial risks. While reducing the probability of operational errors and improving early detection of failures, it also introduces new vulnerabilities related to software, integration, technological dependence and cybersecurity.
Understanding this new risk configuration is essential in order to design insurance and maintenance strategies that keep the technical claims under control. Collaboration between engineers, insurers and plant managers will be key to take advantage of the benefits of modernization without sacrificing operational resilience.
If we are to draw a conclusion from all of this, we could say that greater automation generally leads to lower operating claims that are the result of human error, but technical and interruption risks can increase if they are not properly managed. This is why our role as risk engineers is extremely important when assessing the degree of plant automation so that we can work hand in hand the client to identify and improve the risks presented by this new era.
Author of the article:
Fernando Quintana is part of the Services Engineering team at MAPFRE GLOBAL RISKS. He is a mechanical engineer with 17 years of experience in engineering, mainly in the maintenance and processes sectors. He has spent the last four years working in the insurance sector.
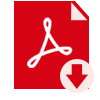