admin | 15/04/2021
The European Commission has set a “zero emissions” target for CO2 by 2050, and the cement industry—the main component of concrete—has a great challenge ahead, as manufacturing it produces 8% of worldwide emissions and 5% of emissions in Spain. We analyze the situation in the sector and its progress towards a more sustainable situation with the collaboration of José María Carrau, territorial representative of ANEFHOP (Spanish National Association of Ready-Mix Concrete Manufacturers).
Concrete is the second most-consumed product in the world, behind only water, and is the basic pillar of most homes and practically all transportation and supply management infrastructures. Its industry is closely linked to the cement industry as it is the main binder of this material, along with aggregate components and water. The cement production process, which uses kilns at very high temperatures (around 1,400° C), is associated with emitting high levels of CO2 into the atmosphere, which, in the international context of the climate neutrality objective, has forced the sector to commit to a roadmap aligned with this purpose, setting 2050 as a deadline in Europe. “Cement, until now, has used manufacturing methods with high emissions, but the industry has been working for many years to reduce them. The key point in the process are the high temperatures required to manufacture clinker, and the idea is to replace it with other additives with similar characteristics,” explained José María Carrau, ANEFHOP’s regional delegate. “The concrete industry will therefore have to design new dosages and get the full potential of their properties. It can certainly be a very interesting time of development,” he stated.
Advances in sustainability
Despite its large scope, the concrete industry is very local and responds to surrounding areas’ needs. This characteristic, together with its on-demand production, means that it has inherent sustainable qualities. “Every concrete factory produces only when there is an order because it has to be delivered fresh. This means that it uses exactly what is needed in terms of raw materials and does not consume an extraordinary amount of energy,” Carrau explained. In production processes, companies have made remarkable progress in reprocessing waste. “We have achieved zero discharge of liquid waste at our facilities since we have been implementing water reuse—to wash vehicles, for example—for years. To this end, we have settling basins that can even extract water from a supply that the builder has not fully used,” the expert confirmed.
Another established practice in the sector is recycling focused on reusing waste from other industries. “For the concrete that comes from structures that no longer are used and are demolished, by regulation, it is accepted that, when properly separated from the steel, it can be crushed and become an aggregate that contains all the set cement, so it can be used to produce new concrete,” Carrau stated. Although he noted a difficulty. “The problem is fundamentally financial, as there are not many demolitions of structures and a more expensive extraction process is required. However, in a few years, this situation will likely change. Although the technology and regulations already exist.”
Sustainability and lines of research
For years, the cement industry has been actively working to improve its environmental impact, and in the last 30 years, it has reduced its total CO2 emissions by 27%. With the signing of the European Green Deal, these aspirations have become a commitment undertaken by all European Union member states. For the cement industry, the first step is to reduce emissions by 43% by 2030 across its entire value chain. Various measures have been taken to achieve this, such as using alternative decarbonated raw materials and using recycled waste and by-products from other processes.
“The cement and concrete companies themselves are heading up important research centers that have already recorded advances, such as environmentally-friendly concrete and solutions that require less cement,” the expert explained. As examples, he also cited improvements in the practicality of the material itself, as in the case of those that can filter water and redirect it under the pavement for new uses, which, in addition to the sustainable component, would prevent puddles.
“There is also an initiative that has been given quite a bit of visibility, which is the ability of concrete to absorb and store carbon from the atmosphere. Some studies demonstrate this absorption capacity. And there are success stories. They are, shall we say, inherent qualities. For example, concrete surfaces can contribute to heat management,” he added, referring to CCUS (carbon capture, utilization, and storage), a technology that has already advanced on a pilot scale in developing oxy-combustion and post-combustion capture techniques and using microalgae to absorb CO2 and grow biomass (which can be used within the industry itself, as a fuel for kilns or in agricultural applications).
Other lines of research are being carried out in the additive phase. Clinkers are being developed that require less limestone in their formulation, thus requiring less energy input. Although due to their properties, they cannot be used in all types of structures.
Carrau notes that, outside of the cement process, the concrete sector’s greatest weakness lies in transportation, where the greatest emissions are produced. So it is relying on the zero-emission vehicle industry (electric, hydrogen, or a combination of both) to significantly reduce this figure in the proposed timeframe, as has been achieved in other areas of its operations. “From concrete manufacturers’ standpoint, we have been working for years to reduce CO2 emissions in the manufacturing process in every aspect of the process and the sustainability of the process itself, making it a clean activity. This is being achieved with zero liquid spills, aggregate reduction (dust emission into the atmosphere). It has been much hard work, and we are getting there,” Carrau asserted. “I think we are making progress and will be able to reach the 2050 deadline in markedly improved conditions,” he concluded.
Article contributor:
José Mª Carrau Criado is an architect, specializing in construction, with a degree from the Escuela Superior de Arquitectura de Valencia (March 1983). He worked as a freelancer from 1983 to 1987.
Delegate of the Spanish National Association of Ready-Mix Concrete Manufacturers since March 1987. The current scope of his Delegation: The regions of Castilla La Mancha, Valencia, and Murcia.
His functions include technical guidance, holding technical workshops, expert appraisal for supply incidents, participating in Certification Committees, and collaborating with the government to develop technical regulations. He has collaborated as an expert in different working groups in drafting the EHE-08 Instruction. He also participated in drafting the Structural Code in the Execution Working Group.
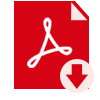