Remote inspection enables MAPFRE GLOBAL RISKS engineers to connect live with their counterparts from our customers’ companies, regardless of where in the world they are, and provide them with real-time advice.
Eduardo García Mozos, director of the Engineering Area at MAPFRE GLOBAL RISKS, explains in this article and in the video that accompanies it how this service is managed during the risk inspections that this department carries out regularly and the multiple advantages it entails that undoubtedly result in benefits for the customer.
The MAPFRE Global Risks Engineering Area is responsible for technical risk assessment for a more refined underwriting, and it is a valuable contribution to the client via recommendations for improvement and services. To develop its functions, knowledge of the facilities is essential through a process of study, analysis and assessment in which the engineer’s visual connection with the risks is essential.
We, risk engineers have traditionally carefully prepared risk visits to travel to sites, literally, anywhere in the world, and carry out the required on-site visual inspections.
The MAPFRE Global Risks Engineering Area is responsible for technical risk assessment for a more refined underwriting, and it is a valuable contribution to the client via recommendations for improvement and services.
The circumstances occurred in March of last year, have made travel and meetings and technical visits impossible; however, the business continues under traditional underwriting processes. All this has meant that we are in a process of incorporating a technology that, like many other changes, surely will become more and more common in our tasks: remote or hybrid inspections as an alternative to physical inspections and a tool to provide customer service.
Remote or hybrid inspections combine a field visit, now conducted by an appointed engineer who knows the facilities and can interact in real time with one or more experts located on the other side of a screen. Inspections are given more flexibility, and new advantages are created both for the client and for us. Some of the benefits of using this technology are as follows: increased productivity as inspections focus on matters of greatest interest to both parties and time is reduced; optimized travel; better diagnostics, to improve technical assistance with the participation of remote experts in the diagnosis, building a new channel of communication with the client, being able to increase the number of visits and conducting a more exhaustive risk monitoring.
The circumstances occurred in March of last year, have made travel and meetings and technical visits impossible. All this has meant that we are in a process of incorporating a technology: remote or hybrid inspections as an alternative to physical inspections and a tool to provide customer service.
Another important benefit is to be able to incorporate training engineers as followers of remote visits in real time.
Therefore, the use of technology represents a technical and client relationship advantage.
Mechanism:
Based on software for smartglasses, smartphones, Android/iOS tablets and PC/Mac, information is shared between the client and our engineers wherever they are located.
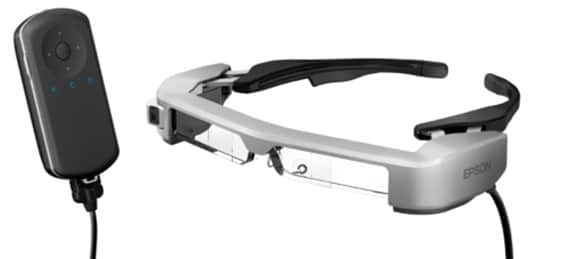
Smartglasses for remote inspections
This information in text, image, video and voice format is perfectly documented and traced.
Using the software, the process is simple and robust. Clients receive a connection link on one of the above devices and experts can begin to see and interact with the client just as they would, if they were at the client’s facilities.
One or more risk engineers connect through remote direct video assistance to assess and control risks at any type of facilities, processing plants, warehouses, workshops, electrical/hydraulic rooms, etc., from any country in the world.
Using the software, the process is simple and robust. Clients receive a connection link on one of the above devices and experts can begin to see and interact with the client just as they would, if they were at the client’s facilities.
One or more risk engineers connect through remote direct video assistance to assess and control risks at any type of facilities, processing plants, warehouses, workshops, electrical/hydraulic rooms, etc., from any country in the world.
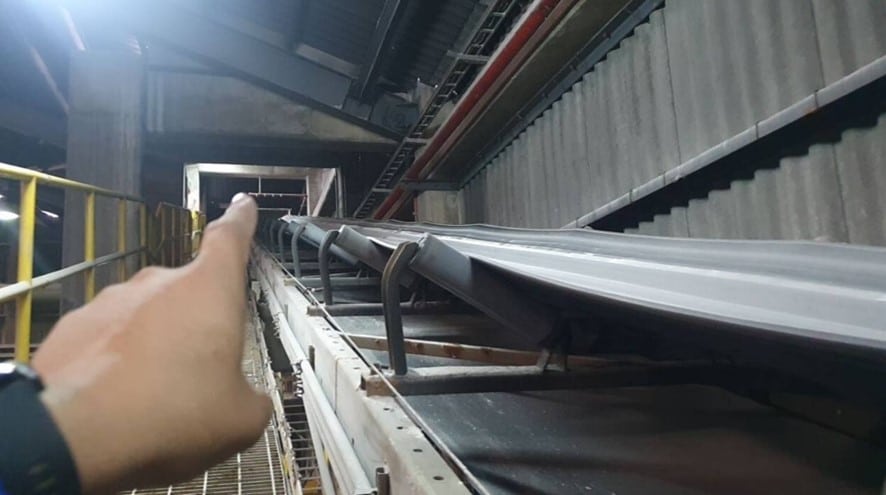
Remote conveyor belt inspections
Engineers with expertise in fire protection systems, equipment maintenance and business continuity, from the industry sector, energy, oil & gas, construction and mining specialties, will be able to assist hardware carriers (smartglasses, smartphones, tablets, Android/iOS or PC/Mac) anytime and anywhere.
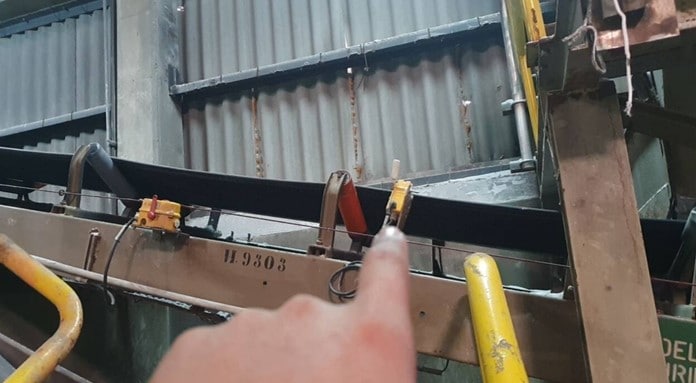
Detail of conveyor belt displacement sensor by remote inspection
The client and the person appointed to handle said hardware can easily resolve any incident related to their assets with real-time assistance.
In short, wherever the risks are, using the remote video support software, the step-by-step performance of work procedures guided by an engineer, and a wide range of simple or complex compatible devices (hardware), we can communicate and interact with any client in an integral manner and guarantee a suitable and documented execution in all types of inspections: technical risk visits, fire safety systems verifications, optimization of maintenance systems for Fire Protection Installations, thermographic diagnostics of electrical installations, complete audits of electrical installations or supervision and monitoring of works, as well as providing recommendations for improvement, and monitoring them closely.
This technology is being tested by the innovation team in the engineering area and will be progressively incorporated into our activity as much as we can take advantage of its efficiency.
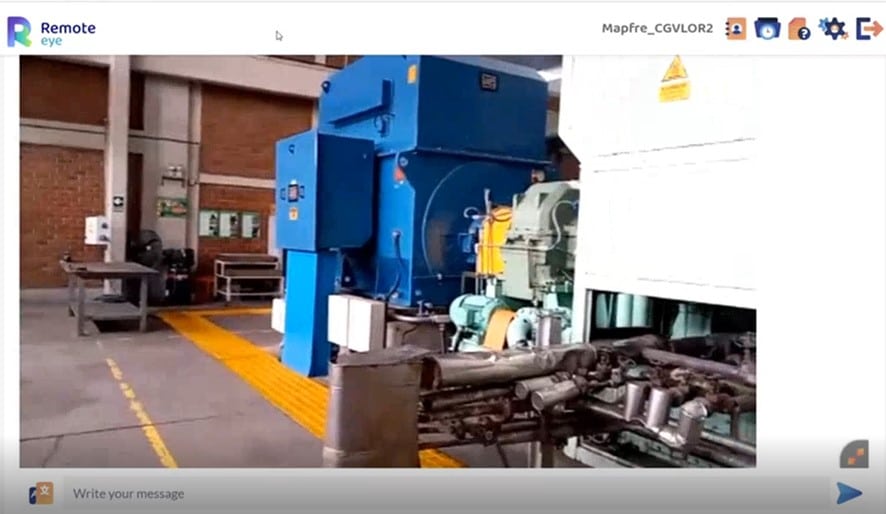
Remote inspection software – Turbine Image
This technology is being tested by the innovation team in the engineering area and will be progressively incorporated into our activity as much as we can take advantage of its efficiency.
This article was written with the collaboration of…
Eduardo García Mozos, Engineering Manager at MAPFRE Global Risks.
Diego Sio, Risk Engineer at MAPFRE Global Risks.
Eduardo Sánchez, Risk Engineer at MAPFRE Global Risks.
Related articles: Tele-inspection and remote risk control
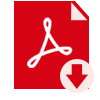